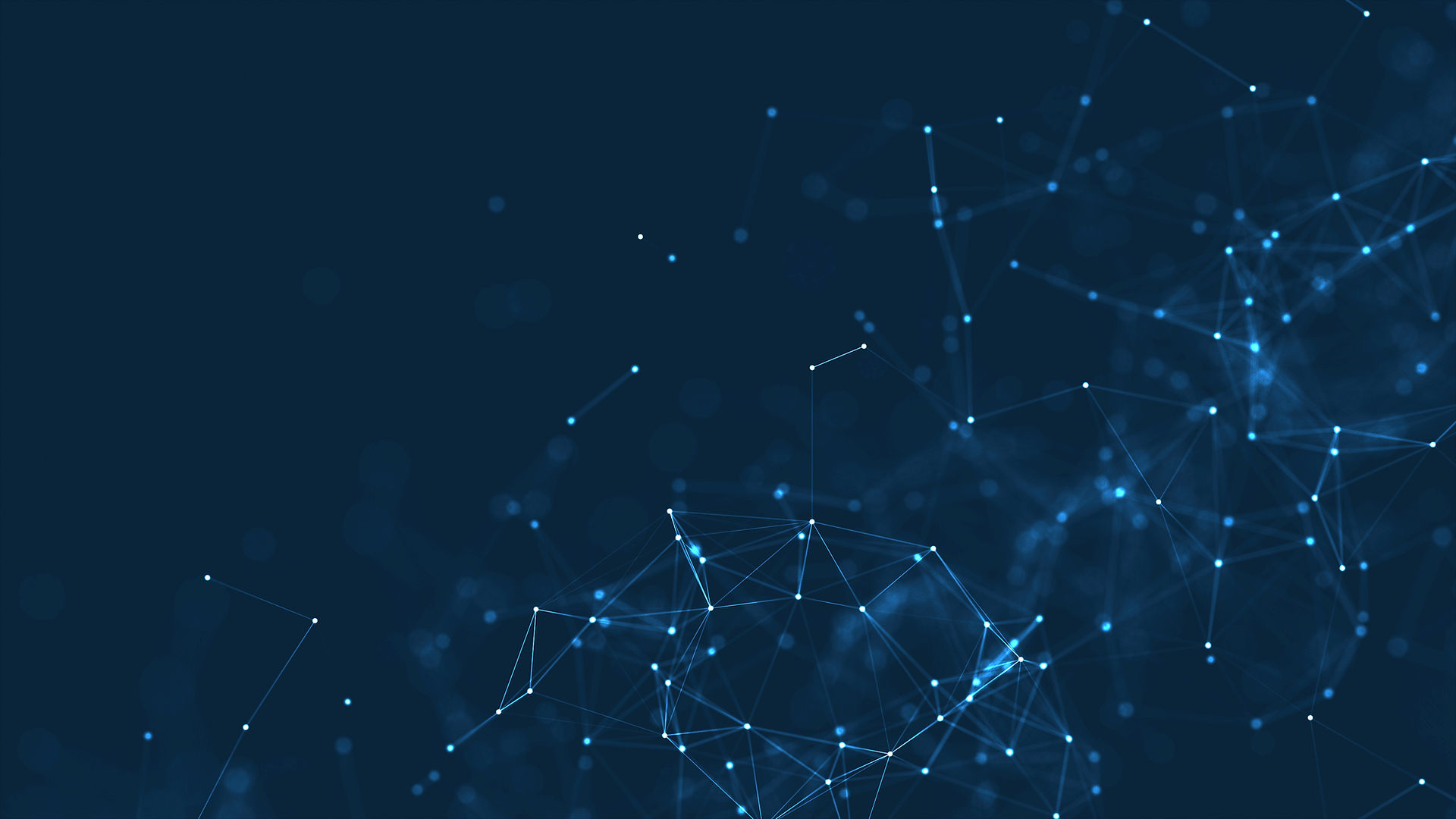

Pellet Firing Furnace - Pot Grate
The Pot Grate is a laboratory-scale furnace used to simulate the thermal processes involved in iron ore pelletizing, allowing precise evaluation of the physical and metallurgical properties of fired pellets. It replicates, under controlled conditions, the full range of thermal treatments experienced in industrial traveling grate furnaces, making it an essential tool for predicting real-world pellet behavior and validating thermal recipes for different ore blends, additives, and binders.
It is a strategic piece of equipment for R&D departments, process engineering teams, quality control laboratories, and industrial project development, as it provides critical data for process optimization, raw material validation, and performance benchmarking.
Pot Grate Operation
A typical Pot Grate test cycle includes several well-defined stages:
1. Up Draft Drying (UDD)
2. Down Draft Drying (DDD)
3. Pre-Heating (PH)
4. Firing (FIR)
5. After Firing (AFIR)
6. Cooling (UDC)
Each of these phases requires tight control over key thermal and fluid-dynamic variables, including:
• Temperature profiles (ramp-up and cooling curves);
• Bed pressure differential;
• Airflow direction and distribution (upward/downward);
• Gas flow rates;
• Oxygen concentration during firing stages;
• Time of exposure at each phase.
Advanced Automation Requirements
The performance of a Pot Grate is directly dependent on the accuracy and reliability of its automation and instrumentation system. Because pellet quality is extremely sensitive to small fluctuations in operating conditions, even minor deviations in temperature or airflow can significantly distort test results.
As such, Pot Grates must be equipped with:
• High-precision sensors and actuators;
• PID-regulated control loops;
• Secure, real-time supervisory systems (SCADA);
• Data logging, alarm management, and historical reporting tools.
With the ongoing evolution of industrial technology, regular retrofits and system upgrades are necessary to keep Pot Grates performing at their best. This includes the replacement of outdated controllers, integration of modern communication protocols (e.g., Modbus, Profibus, Ethernet/IP, OPC-UA), and the adoption of more intuitive and flexible interfaces. These updates extend equipment life, enhance data integrity, and improve repeatability of the tests.
ControlVix Experience
ControlVix is a recognized leader in automation and instrumentation systems for the pelletizing industry, with proven expertise in Pot Grate applications. Since 1986, our engineering team has participated in all major Pot Grate retrofit and installation projects for VALE and ArcelorMittal, both in Brazil and internationally.
With over 28 years of hands-on experience in this specific type of equipment, our scope of work includes:
• Complete solutions (mechanical, electrical, and software);
• Custom development of SCADA and DCS-based control logic;
• Installation and calibration of industrial sensors for temperature, pressure, flow, and gas composition;
• Commissioning and validation in laboratory and pilot plant settings;
• Operator training and technical support tailored to laboratory and process engineering teams.
Our focus is on delivering high-performance, future-proof automation solutions, aligned with the latest standards of Industry 4.0, ensuring that laboratories and R&D centers can rely on consistent and accurate results for strategic decision-making.
The Pot Grate is not just a testing furnace — it is a key strategic asset for process development and quality assurance in the iron ore pelletizing chain. Its performance depends heavily on the quality of its control systems. With decades of specialized experience, ControlVix is a trusted technical partner, offering complete solutions and long-term support for Pot Grate automation and performance excellence.

